"I'm glad we found you!"
Is a compliment we get often from operators we help.
We’re glad you found us!
Problems are solved efficiently and affordably, we are pleased to provide a valuable service you can depend on.
Trust us with your 3D printer and we won't let you down.
If you need help, simply send us the details using one of the options below, and we’ll take care of the rest.
Repair Examples:
We fix a lot of printers, here’s a small selection of our work:
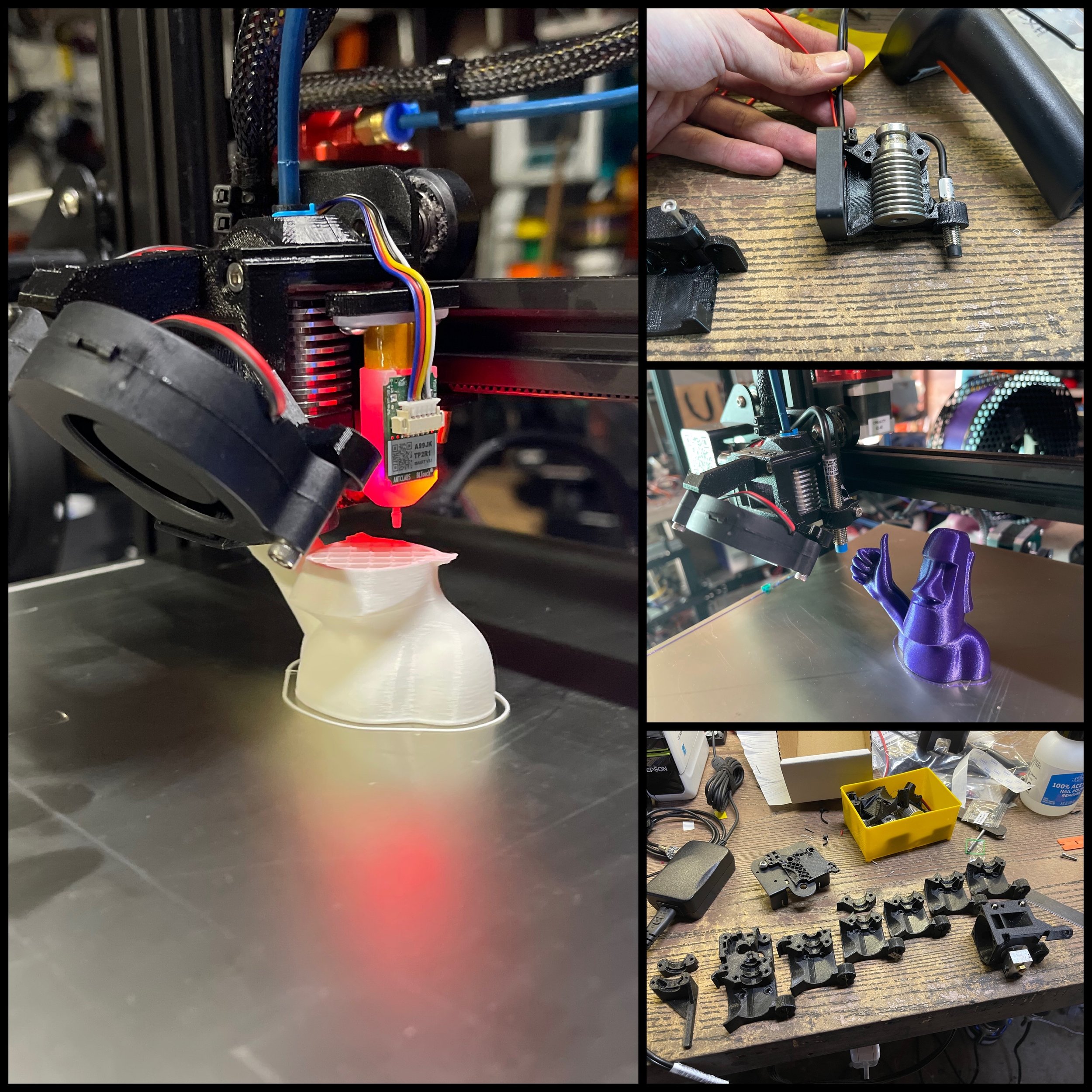
We have several in-house designed drop-in upgrades which we only sell directly, you won't find these anywhere else.
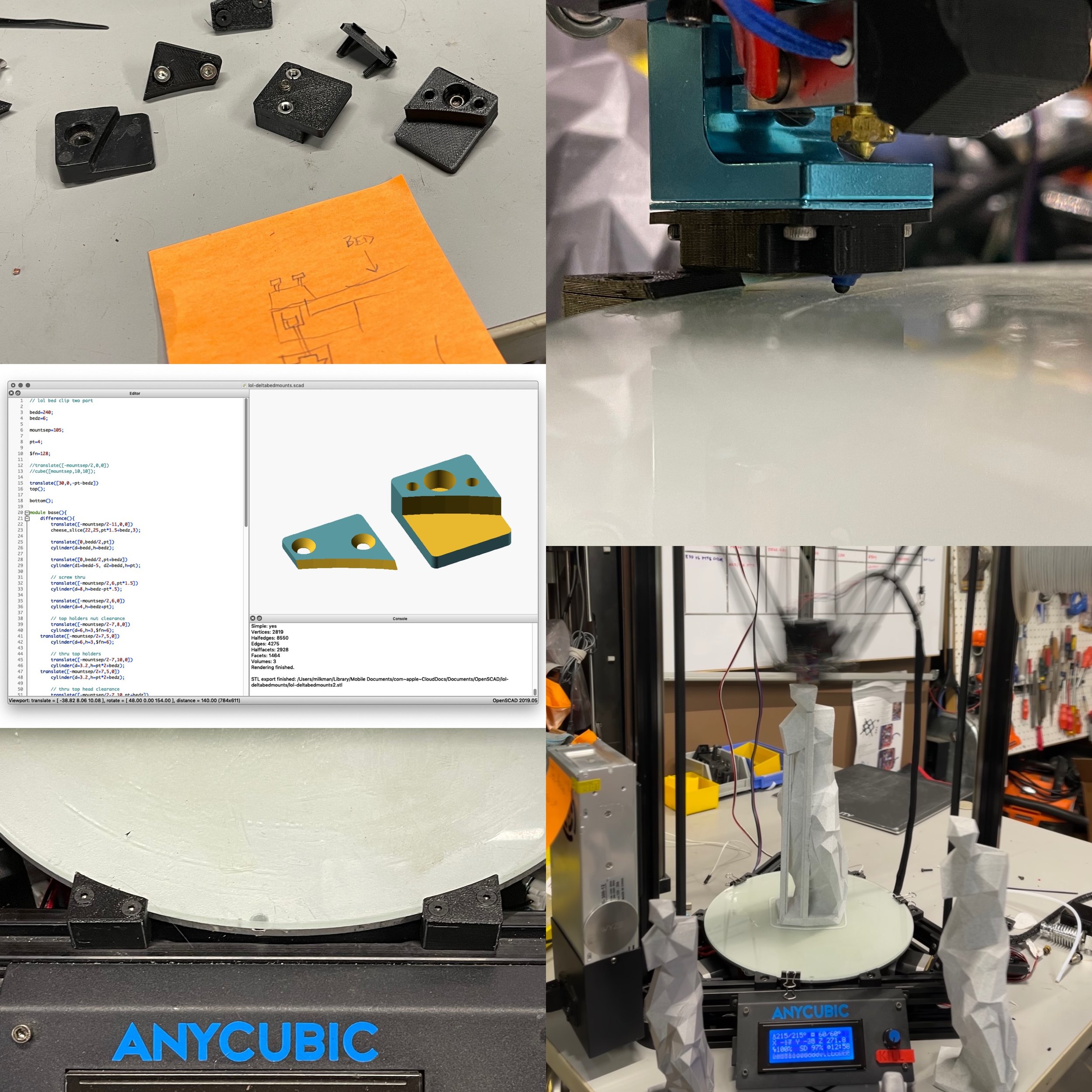
3D Printer problems need 3D Printed solutions.

Visual aids help illustrate problems to our customers, we don't just fix, we educate.

It's the sentiment that counts, not the grammar. 👍🏻

This TERRIBLE guidance from a reputable publication is in direct conflict with the assembly manual for the product which it clones - demonstrates a complete lack of familiarity with the fundamentals, and shows how treacherous "advice" in this market can be.

We have undertaken some lubricous projects, such as a complete, comprehensive retrofit for the MakerBot Replicator chassis to implement Marlin, complete with internalized PSU, and re-designed LCD enclosure.

A Prusa MK3, "totaled" in a topple, completely restored and upgraded to MK3S with MMU2S.

We have solutions borne out of years of experience summed up in simple terms.

We design parts on-demand to address problems, this simple adapter permits clean wire routing on Prusa MK2S printers.

Detail of Hemera mount repair with epoxied square nuts held via improvised SCAD jig.

It is illegal for a manufacturer to refuse service on an opened a device exposing "VOID" stickers, they are meaningless.

Failed Solid State Relay, likely poor QC; the mating of heat-spreader was fouled by a blob of solder, causing accelerated life.
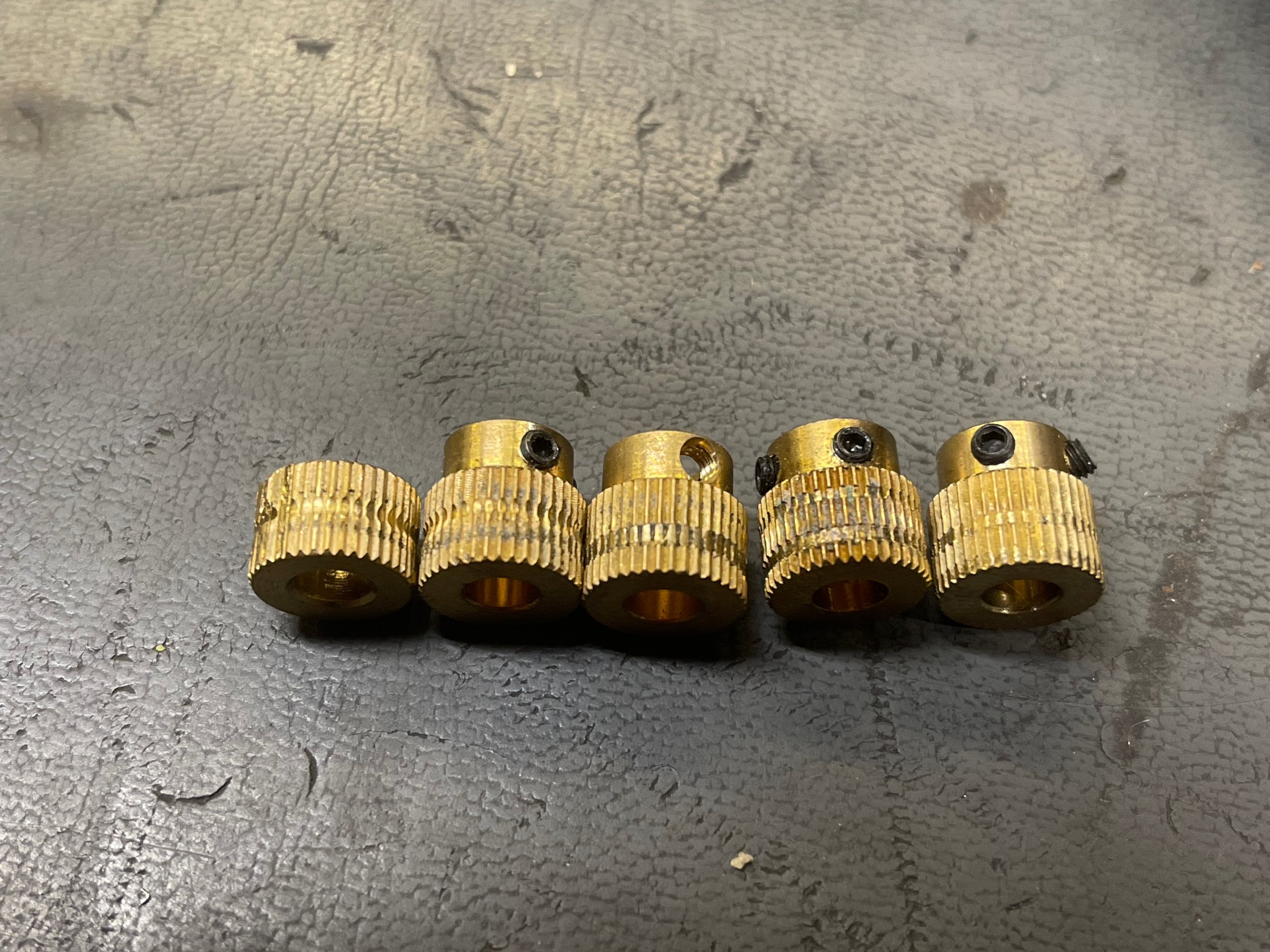
Fouled drive pulleys from various Creality printers, obviously made of brass cheese.

You can spend a lot of money on upgrades and get frustrated making them work, whatever your situation, we will make you proud.

A batch of failed mosfets off a ChithuBoard, we will perform board level repairs where feasible.

Filament scrap stuck in a drive pulley from the Y-Axis of a Prusa MK2S causing head-crashes.
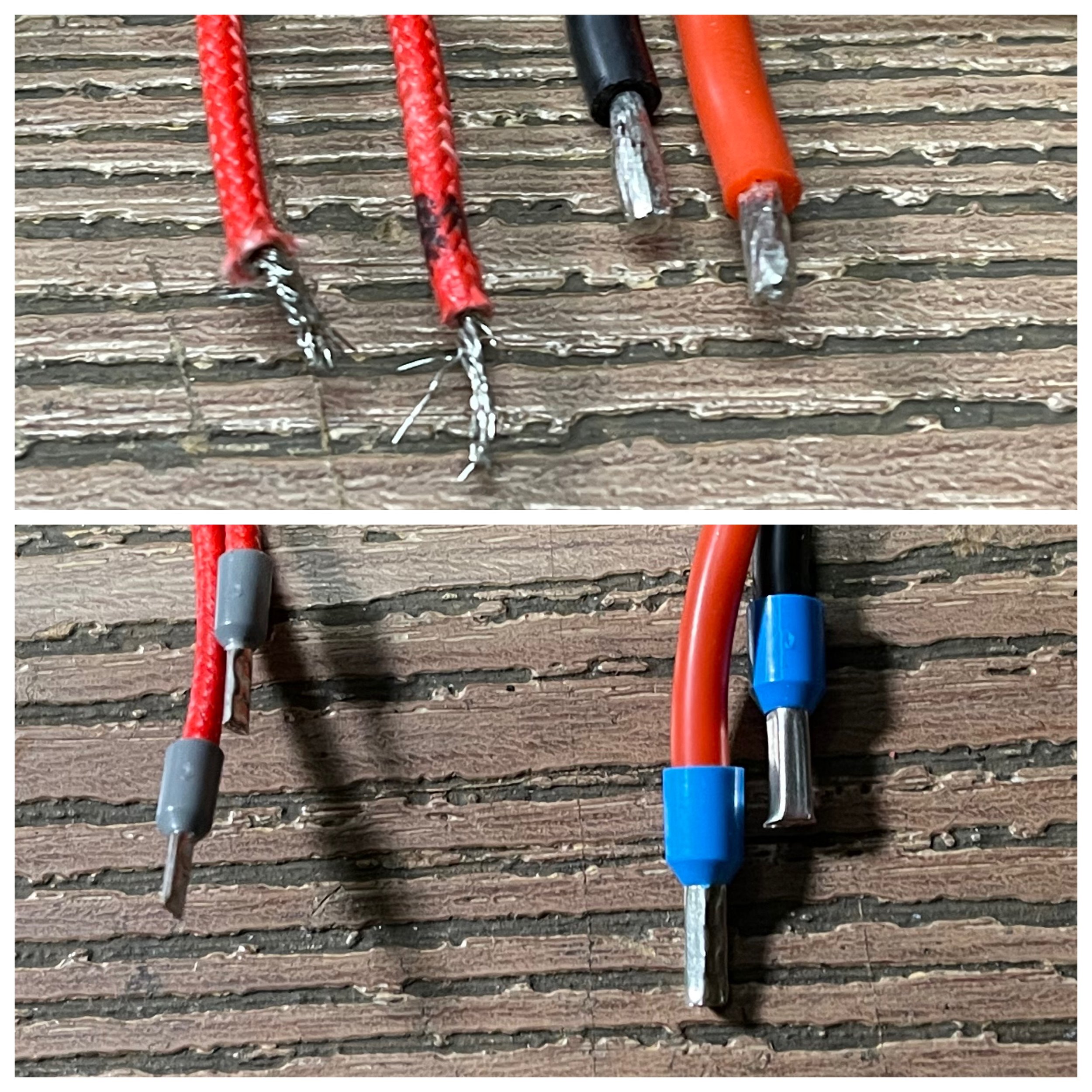
We regularly see bare wires on even new printers, this is generally "ok" but it's a shop standard to always use crimped ferrules to secure stray wire strands that might short.

Lots of nozzles - quality parts, the right nozzle for the application, and regular maintenance will keep you printing, indefinitely.
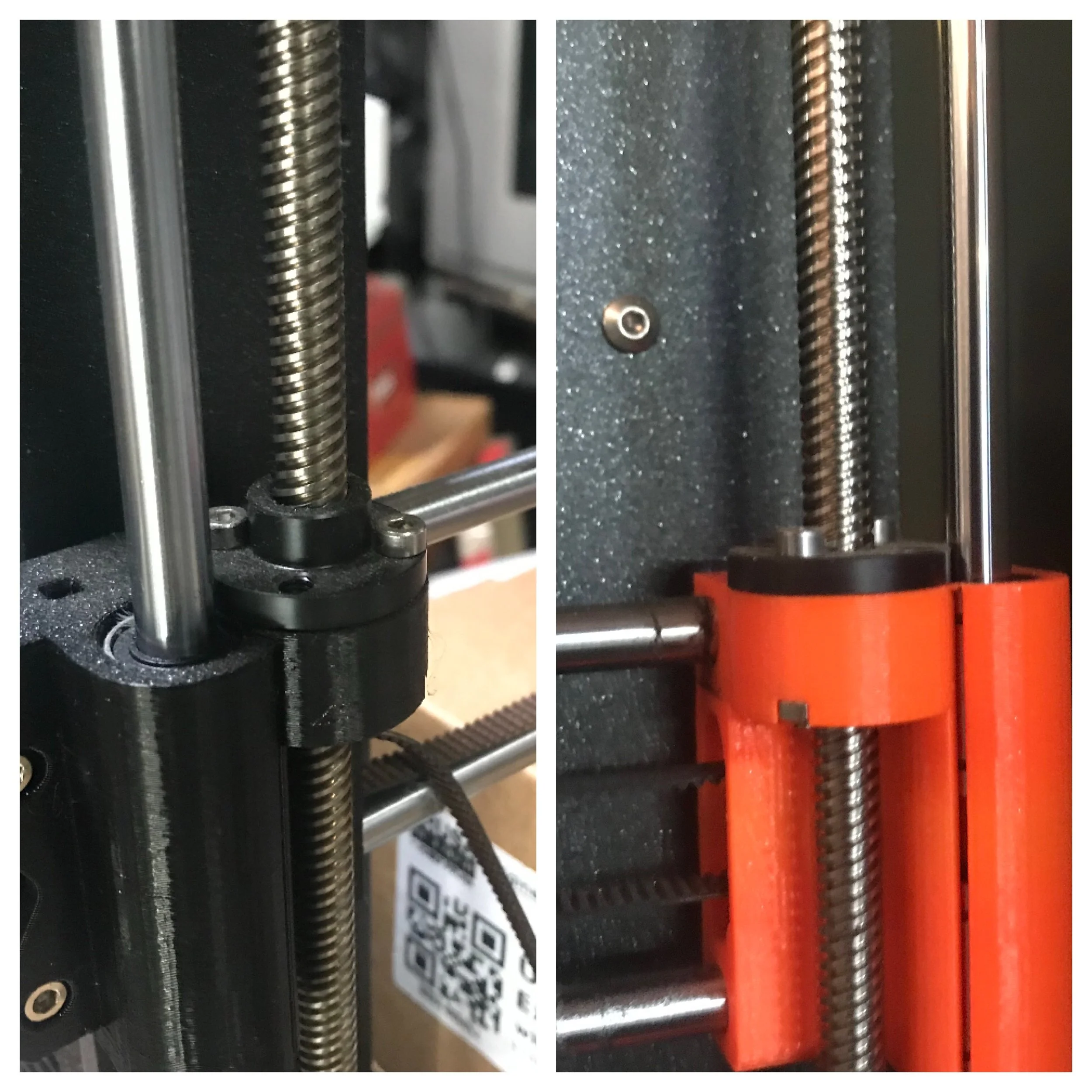
Incorrectly oriented "trap nuts" might work, but it's wrong, and every printer that earns our sticker leaves the shop right.

A common extruder idler lever failure we have seen recently on Creality printers, bad/no QC.

Self-service doesn't always go as planned, but we can get you out of even a serious jam with zero hassle.

Correct hotend maintenance is absolutely essential to long-term success with your printer and will avoid "showstoppers".

Customer commission E3D Volcano install on Creality CR-10S Pro

Our Prusa MK3S 3D printing farm doing 3D printing things.


You can indeed achieve near-resin caliber prints, with a standard FDM printer and a stock 0.4mm nozzle.

Once in a while, we get to just relax...
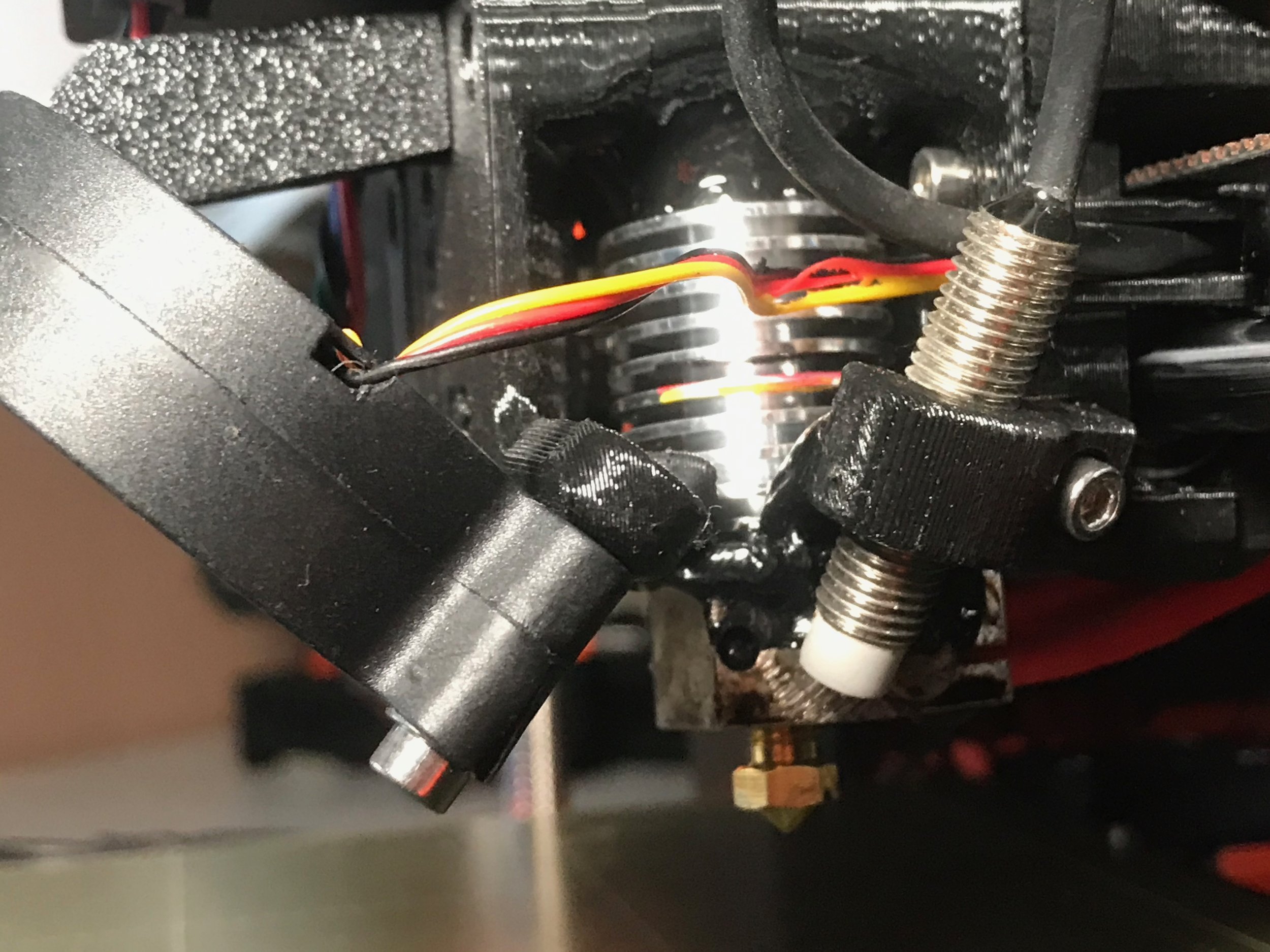
A severely heat-creeped Prusa extruder, incorrect hotend service cascading to take out other parts, we replaced the melted components, mended the fan wires, no big deal. Rapidly recovered and restored into working service at minimal cost.

The MMU2S is a grossly under-appreciated and misunderstood product, we have repaired more than anyone, and used our experience to produce "The MMU2S Theory of Operation" to help operators get their grips with it.
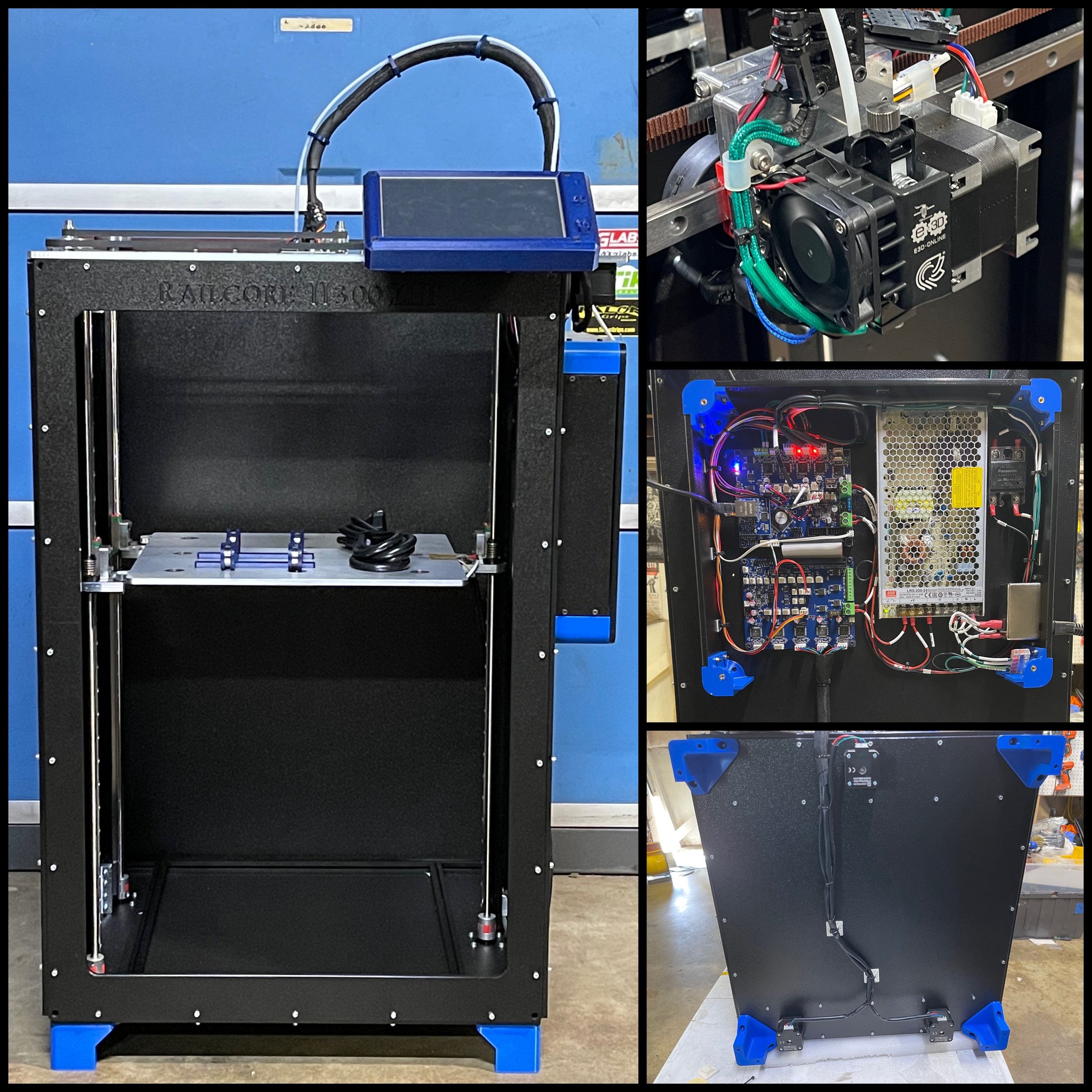
We perform regular commissioning of customer printers, like this RailCore 300ZLT.

The Prusa "wall of pride", Prusa is the only company *constantly* improving a product rather than sell you a new model. It prints its own upgrades - that should be the standard, not the exception.